ALTERNATIVE BUILDING TECHNOLOGY
​
Build Better. Faster. More Cost Effective.
​
LIGHT STEEL FRAMES are assembled in a similar manner to wood platform framing, and have some of the same advantages.
Steel is easy to manufacture and is frequently made from recycled material, which cuts both the environmental impact and the cost to the consumer. Additionally, light-gauge steel is very easy to customize as it can be folded and punched at the factory to exactly meet the client’s specifications. Steel is a great option for clients looking to branch out into other design styles, as this method adapts particularly well to the clean, more minimalist lines and wide open spaces of modern design; lighter cold-pressed steel allows for longer spans (as opposed to the wooden spans possible with wood framing), with even larger spans possible with the thicker, hot-pressed beams. Full-window walls and extended overhangs are also commonly seen with steel-framed structures.
Another upside to steel framing is the precision with which steel parts are manufactured. Because parts are manufactured off-site to exact specifications, clients can be assured that what whatever they specify on their plans will be exactly what shows up on site, with the factory precision greatly reducing the chance of errors made and modifications needed on the job site.
Additionally, when assembled properly frames made of steel are much more durable than those made of wood, meaning that homeowners who choose steel framing typically have fewer environmental-related issues down the line (steel is impervious to mold, mildew, rot and termites, the issues that commonly plague wood structures), and have less to worry about when it comes to their health.
​
While the demand for steel-framed homes is growing, the limited number of builders knowledgeable about this building method and a higher materials cost can make steel framing less appealing to some clients. Also, while steel parts are easy to customize at the manufacturer, they are more difficult to adjust on site, making it harder to make changes on site after the pieces have been fabricated.
​
We are implementing this technology to bulk housing as the time allowed to complete a house will take up to 14 days from inception.
​
WATCH THIS SPACE FOR MORE INFORMATION. BUILDING A BETTER ECO-FRIENDLY FUTURE.
​



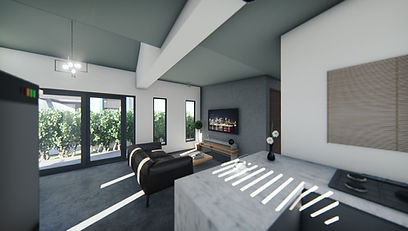
